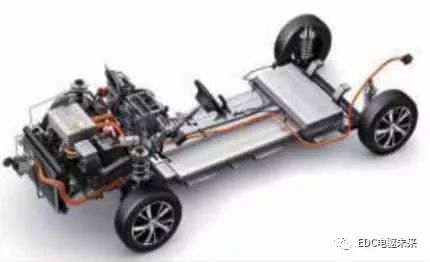
来源 | EDC电驱未来
1、集成化电驱动系统概述
电驱动系统是纯电动汽车的核心,主要包含了高性能动力电机、电力电子控制单元和减速器等部分。机电一体化的电驱动系统的优越性愈发明显,其能量密度大、效率高和维护性低等特点,使得电驱集成化设计在纯电动汽车领域得到慢慢的变多的应用。
最初的电驱动系统不存在集成式设计,图1 示出某纯电动汽车前电驱系统,其驱动电机、电控系统、减速器等部件均单独布置,之间依靠线束等连接件进行连接,从而导致当时的驱动系统十分复杂。随着乘用车行业的发展和相关技术的积累,集成化电驱动系统逐渐成为主流,如图2 所示。很常见的集成化设计包括取消三相线,将电机、电控端子直连,取消水管,将电机、电控水道直连,以及电机壳体和减速器壳体共用等。这些集成设计早些年因为技术壁垒或者成熟度不够的缘故无法实现,现阶段随着技术难点逐渐被攻克,各大整车厂商开始将电驱动系统的深度集成化设计制造作为重要发展趋势。
图1 某纯电动汽车前电驱系统
图2 某纯电动汽车集成化电驱系统示意图
2、电驱动系统集成化的优劣势分析
2.1、集成化电驱动系统的优势
首先,集成化设计可以轻松又有效地减小电驱动系统的体积、降低系统总质量。电驱动系统的各个部件通过整合,整体结构更为紧凑,安装尺寸和所占体积得到进一步缩减;与此同时,各部件之间的连接材料因为集成化设计而大幅度减少,系统质量也得到了降低。
其次,采用集成化电驱动系统的机舱更加简洁,使得汽车各系统布局更加灵活。由于体积减小,整车的乘坐及储物空间得到最大化利用;同时汽车质量的降低在某些特定的程度上也降低了汽车能耗、提升了续航里程。
此外,通过集成化设计,电驱动系统能够降低接口复杂度及成本。电驱动系统集成化有效地缩短了各部件之间的距离,减少了连接件及相应接口的使用,在优化了传输路径的同时也提高了系统的效率;而电驱动系统采用的连接件包含导线和管路等材料,是不可忽略的生产所带来的成本,因此减少连接材料的使用将直接促成电驱动系统成本的降低。
2.2、 集成化电驱动系统的劣势
电驱动系统集成化设计需要多维度开发和能力验证,如图3 所示。其中集成系统导致各部件与空气接触面积减少,为保证各部件处于正常工作时候的温度区间,整个散热系统需要重新设计优化。同时,NVH(噪声振动)、EMC(电磁兼容测试)、安全等性能指标的控制,以及零部件开发协同都是目前整车厂和供应商需要重点攻克的难题 [2]。
图3 纯电动汽车电驱动系统集成化设计
在后期用车方面,电驱动系统的集成化可能对消费者产生不良影响。某些特定的程度上,系统的集成会导致各部件的可靠性降低,集成化电驱动系统各部件的质量控制显得特别的重要;当某个零部件出现一些明显的异常问题需要维修或者更换总成,会导致维修时间和成本增加。
综合来看,电驱动系统集成化对于纯电动乘用汽车行业来说具有积极的推动作用,但是基于现阶段电动汽车供应链的技术水平,集成化过程中的设计和质量上的问题对于整车厂商和供应商来说仍然是巨大的挑战。
3、集成化电驱动系统的应用现状
3.1、二合一电驱动系统
集成化电驱动系统发展之初,结构及形式较为简单,如图4 所示,是将永磁电机和减速器集成在一起,与车桥结合形成一体式电驱动桥。从图4 中能够正常的看到,虽然该系统的连接部分很复杂,但是至少实现了二合一的设计,缩短了各部件之间的距离。二合一这种简单的集成形式也使得电驱动系统整体结构更加紧凑。
图4 纯电动汽车二合一电驱动系统
3.2、 三合一电驱动系统
随着电驱动集成技术的不断演变发展,三合一电驱动系统出现,如图5 所示。主流电驱供应商多采用三合一电驱系统,例如:将电机、电控系统和减速器集成在一起并与车桥相结合的电驱系统;或是针对中小型轿车提供的更加轻巧的三合一电驱动系统,转速可达21 000 r/min,不仅性能优异,而且电能转化效率极为高效。某公司通过平台化设计开发出能够很好的满足不同功率和扭矩的电驱动系统(如图5a 所示),缩短了研发周期。
图5 纯电动汽车三合一电驱动系统
国内对三合一电驱动系统的研究与国外相比起步较晚。表1 示出三合一集成化电驱动系统国内外对比分析表,国内在驱动电机功率密度方面和国外产品相当,而电机控制器功率密度和国外相比有一定的差距;在最高转速方面,国外成熟电驱产品的转速已经超过16 000 r/min,国内则多数在12 000 r/min 左右。随着国内新能源技术的飞速发展,自主品牌电驱动系统也已取得较大进步。例如:某三合一电驱动系统具有高效区宽、IGBT(绝缘栅双极型晶体管)损耗小等优势,满足了不同级别轿车对加速、爬坡等动力性能的需求;某集成化电驱动系统能够实现超高的扭矩,优化后的能耗为15 kW·h/100 km,达到了业界先进水平;图5b 示出的集成式电驱动系统配备了铜转子感应电机、独特拓扑架构设计的电机控制器及大扭矩齿轮箱。
表1 三合一集成化电驱动系统国内外对比分析表
3.3、 多合一电驱动系统
三合一电驱动系统是当前的主流研究对象,但仍有一些公司对多合一集成设计进行了不同程度的尝试。如某公司自主研发了八合一集成电驱总成,在常规三合一模块之外,还集成了五合一电驱动模块:电机控制器、车载充电器、车载电源、高压配电模块以及整车控制器。整个系统结构更加小巧,水冷系统的工作效率也得到大幅提升,但整体结构集成后柔性化程度降低,影响机舱的总布置。
4、集成化电驱系统的发展的新趋势
4.1、 电机高速化
当前市场上电驱动系统的电机最高转速一般在12 000 r/min 左右,但是随着新技术、新材料的发展及应用,加之客户对驱动效率、加速体验的重视及追求,采用更高速的驱动电机成为集成电驱发展的必然趋势。高转速电机能够提高功率密度,同时减小体积、减少相关成本,对于电动车动力性能来说优势尤为明显。现阶段有部分转速超过16 000 r/min 的高速电机已经面市,主要应用于中高端的纯电动车型中。就在近日德国慕尼黑工业大学发布了50000rpm超高速3挡BEV传动系统。
4.2、 多挡减速器
目前全球主流集成化电驱系统多采用电机匹配单挡减速器的架构,其结构相对比较简单,成本较低,但在高转速情况下效率和扭矩会急速衰减,当电动车达到极速后没有提升的空间,因此,经济性不高。而多挡化设计能够使电机尽量工作在高效率的转速区间,同时兼顾其动力性能和经济性,特别是在极速状态以及低负荷条件下,挡位的切换能够确保驱动电机多数情况处于高效率工作点。随着将来技术成熟度的提高和成本的降低,多挡减速器(如图6 所示)必然会成为更多集成化电驱动系统的选择。
图6 2挡集成电驱系统
4.3、 平台化设计
汽车产业是典型的规模经济产业,汽车产品平台化设计能够有效地降低研发成本,缩短上市周期。根据不同转矩、功率需求以及不同级别的车型,可以规划不同的系列化平台电驱动产品,如表2 所示。通过平台化设计集成电驱动系统,能够更好的降低各部件的采购成本,实现技术经验共享。纯电动乘用汽车市场需要在短时间内产生规模效应、增量降本,因此集成化电驱动系统向平台化设计发展是大势所趋。
表2 永磁同步平台化集成电驱动系统
5、结论
随着新能源汽车技术的突飞猛进,零部件集成化设计慢慢的变成了必然趋势,而集成化的电驱动系统就是当今时代飞速发展的产物。文章主要分析了集成化电驱动总成与普通电驱动系统相比的优点及弊端,并总结了当前纯电动乘用车市场集成化电驱动系统的国内外应用实践。根据当前电驱动系统集成化设计的前沿发展的新趋势,高速化、多挡化、平台化的三合一电驱动系统在近期内都将是纯电动汽车产业重点研究的技术核心。